MEMBRANE FABRICATION
During the manufacturing phase of a project, Span Flex’s 42,000 square-foot membrane manufacturing plant has efficient capacity and a highly trained staff working with tensile fabric materials, such as PTFE, PVC, and ETFE film. Once final engineering has been confirmed and shop drawings are produced, prestress PTFE or PVC fabric membrane is cut and welded to generate final panel sizes to be installed in the field. This in-house capability allows for Span Flex to meet accelerated schedules and regulate production quality. As a full-service specialty contractor, this manufacturing capability separates Span Flex from other U.S. based companies. Span Flex also utilizes manufacturer recycling programs for PVC and ETFE film in addition to pre-fabrication processes that minimize waste. Due to the lightweight nature of the fabric, it’s also easily and efficiently transported, making it one of the most exceptionally sustainable building materials available for roofing and façade applications.
Span Flex currently has one of the largest (35m x 5m) automatic cutting tables in the tensile structures industry allowing custom full-size fabric patterning, plotting, cutting, scanning and digital services for precision and accuracy.
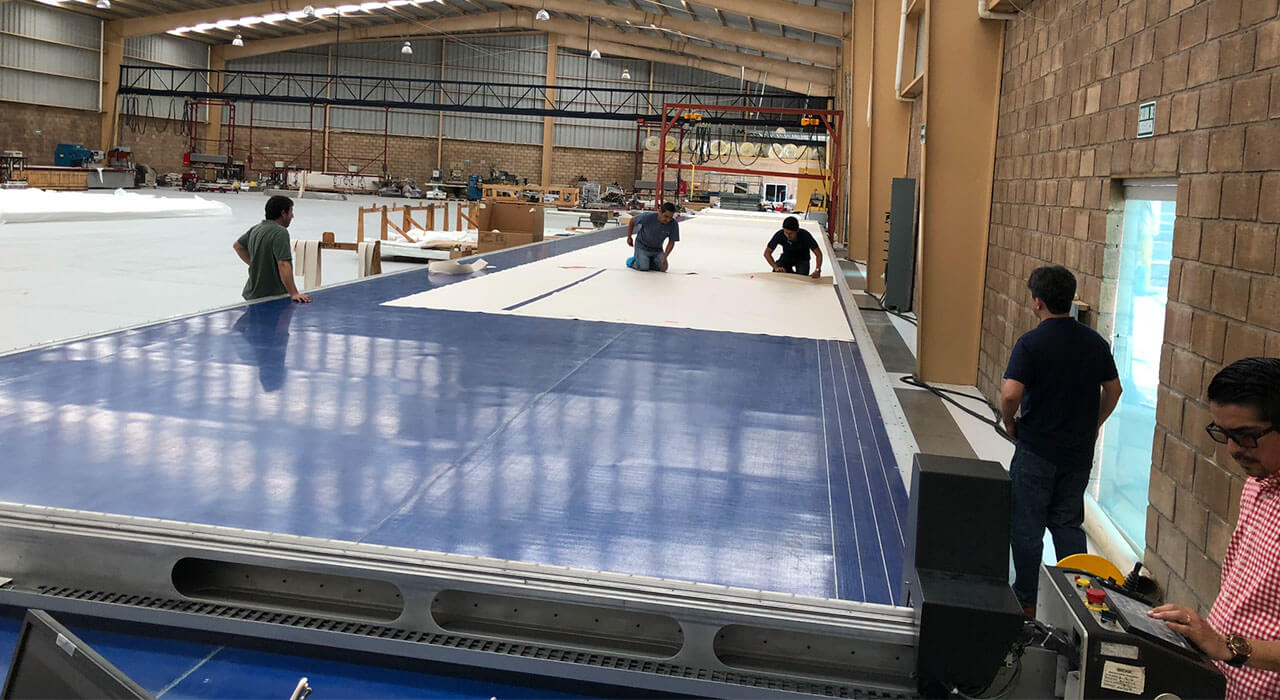